Key Takeaways
- Agility and innovation drive success: An accelerated timeline pushed the team to adopt Lean methods and virtual tools, delivering the project on time with national recognition.
- Collaboration in the virtual era: COVID-19 reshaped teamwork, fostering new efficiencies, empathy-driven collaboration, and human-centered solutions that endure today.
- Sustainability and future readiness: The project focused on sustainability, adaptability, and strategic planning to meet long-term community, environmental, and technological needs.
Lessons learned and Lean tools aid in future projects
When the COVID-19 pandemic brought the world to a halt five years ago, Page designers were in the early stages of expanding healthcare services for children in Austin, Texas. But as the pandemic unfolded, the project faced an unprecedented challenge: not only was a month lost due to the initial disruption, but the construction timeline for the new Texas Children's Hospital North Austin Campus was accelerated by a staggering eight months. Meeting this ambitious new deadline required a complete rethinking of traditional workflows.
What emerged was more than just a project delivery success story. It was a case study of resilience, adaptability, and the power of innovation under pressure. The team, which included Page, Texas Children's, and contractor McCarthy Building Companies, not only met the ambitious new deadline for the Texas Children's Hospital North Austin Campus but did so with national recognition for excellence in healthcare design and construction.
More than adapting to crisis conditions, Page embraced Lean methodologies, virtual collaboration tools, and new efficiencies that have since become integral to its approach. The lessons learned, about agility, communication, and strategic decision- making, continue to shape Page’s work today.
This is the story of how a global disruption catalyzed a new way of thinking about project delivery, one that prioritizes resilience, efficiency, and human connection.
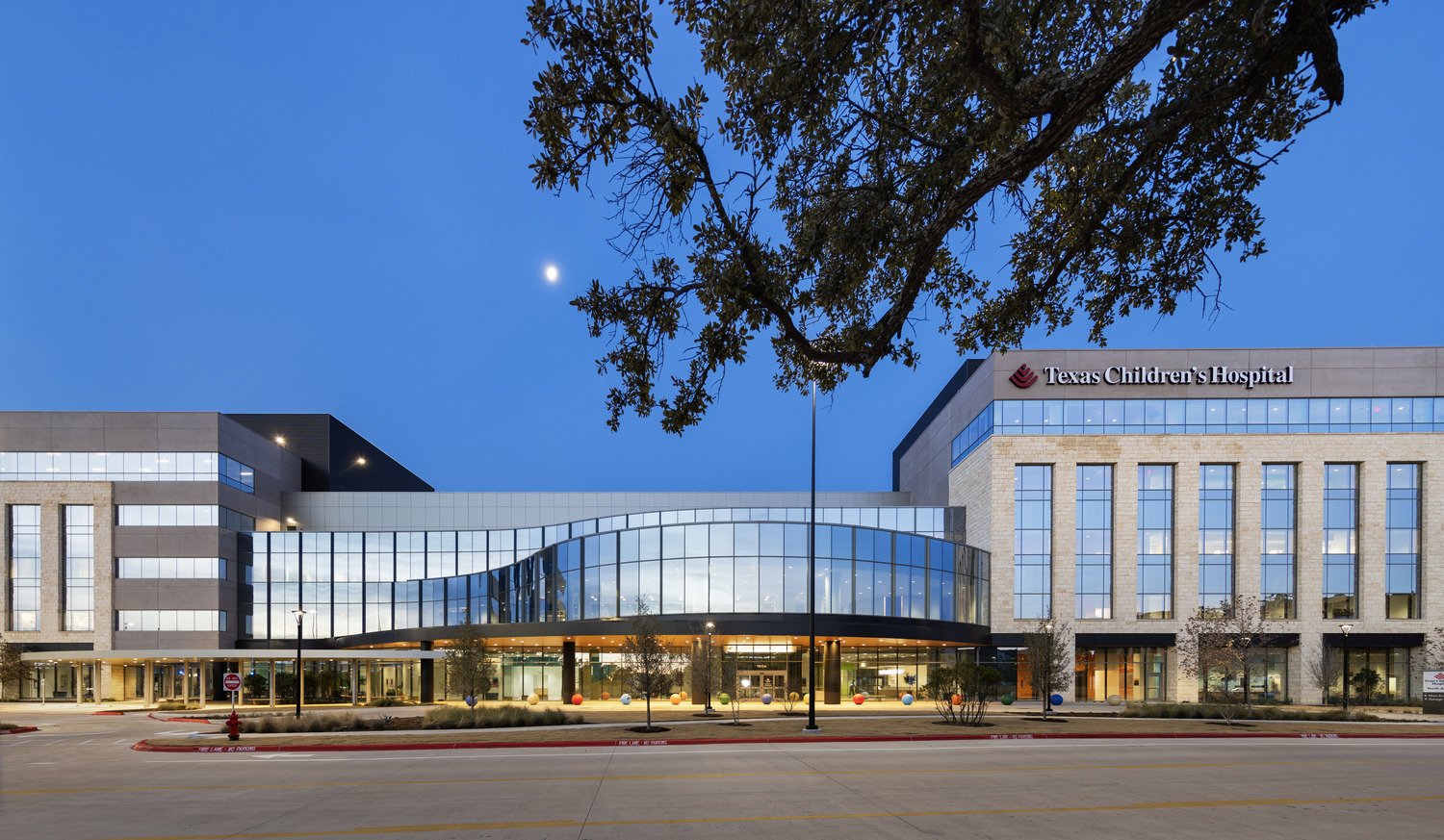
Impact of COVID-19 Pandemic
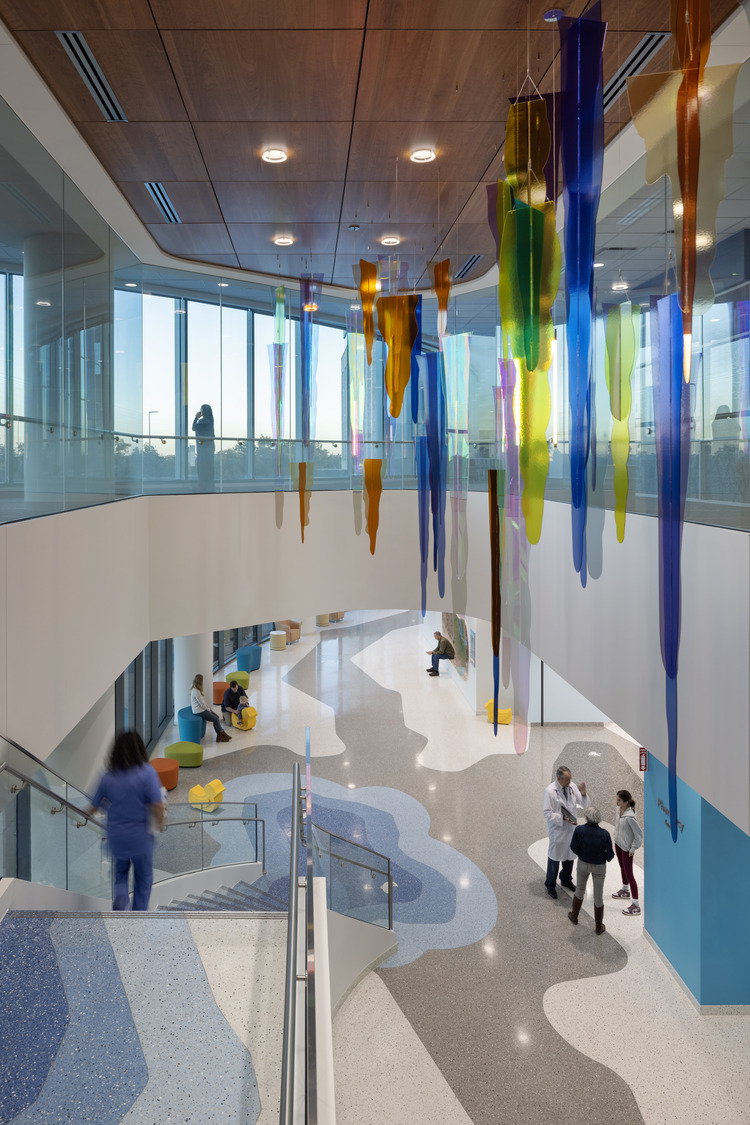
Even as businesses have moved past the immediate disruptions of the COVID-19 pandemic, Page designers continue to incorporate award-winning insights gained from the virtual environment into current and future projects.
Lean efficiencies and lessons learned during the global pandemic from designing and constructing the 52-bed, 365,000-square-foot children’s hospital played a pivotal role in Page’s collaborative and performance-based approach.
Beth Carroll, AIA, LEED, AP, EDAC, Principal, and Regional Healthcare Director, who was the lead healthcare planner on the Texas Children’s Hospital project, said COVID-19 enabled the team to quickly embrace technology, such as virtual walkthroughs and virtual tabletop simulations, as well as tools to edit architectural drawings.
Flexibility was also key in finding innovative ways of working together.
“We realized how resilient we were and how we were able to adapt. It was quite the balance, but it was interesting how we all made it happen,” Carroll explained.
The end goal was developing an uplifting space for patients, families and staff that assists in healing and recovery.
A New Normal: Virtual Collaboration and Human Connection
Working in a home environment like the rest of the world became the new normal and required innovative ways to maintain effective communication.
Gone were personal body language cues and interactions during in-person meetings. Instead, teams used new ways of interacting not to lose that personal connection.
One of those tools was embracing Lean, a process of eliminating waste and improving efficiency, which teams were already using on a smaller scale.
“It became an interesting journey of how we all worked together and also got to learn from each other on a personal level,” Carroll said. “We had kids and pets occasionally entering the screen, and it just humanized everybody.” She noted that many team members faced similar challenges, which fostered empathy and strengthened the team’s cohesion.
At the time, Carroll’s daughter was 7, and her son was 4. Her husband also was working from home.
“What many people didn’t see when I was on camera was my daughter in the corner of the same room doing online learning. In between meetings, I would help her with her school work,” she shared. “My son, on the other hand, was at my feet crawling around. Keeping him occupied was a little more challenging, but again, we had many other people on the team who also had families at home. We gave each other a lot of grace through it.”
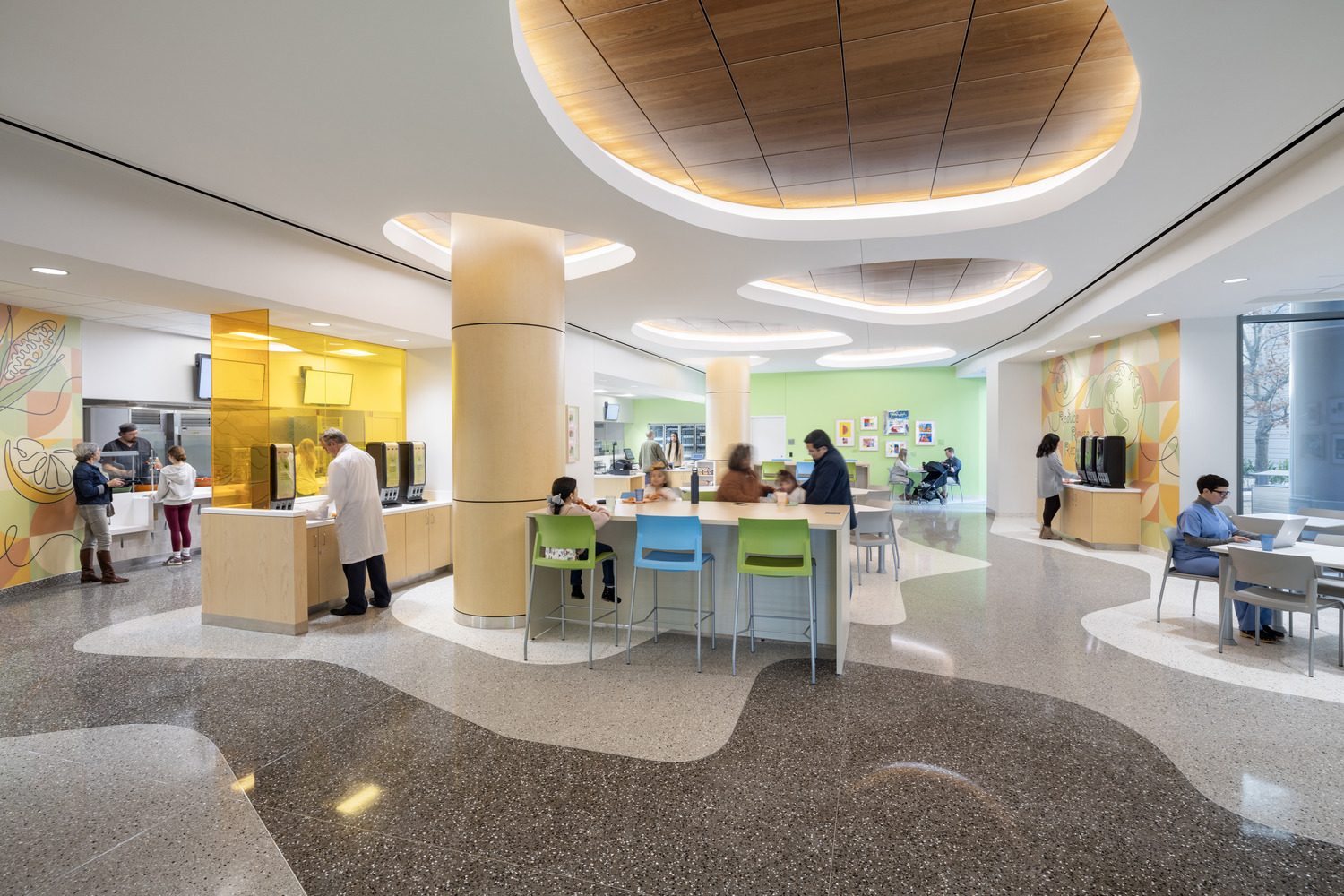
Lean as a driving force in project success
Lean methodologies, stemming from the Toyota Production System1 original manufacturing philosophy, were embedded into the team’s daily routine, reinforcing accountability and efficiency. The strategic use of Pull Planning, a scheduling technique designed to keep teams focused on end goals, played a critical role in maintaining project momentum.
“We leaned into our Lean methodologies and tools and put all of that into a task management system (Pull Planning), so we all saw what everybody needed to accomplish on a week-to-week basis,” Carroll said. “You also saw that if you didn’t finish your part, you kept other people from completing their pieces.”
A Team Charter, one of the first tools that aided in project completion, outlined project goals and the path forward, emphasizing open communication, mutual trust and respect, and collaborative innovation. Page had a great working relationship with the hospital system after working on previous projects and was able to develop the charter at an in-person meeting prior to COVID-19.
“We had a combination of a great client that was responsive in giving us feedback immediately and collaborating with us. We also had great project leadership. They worked with everybody on a personal level,” Carroll said.
To get used to the new virtual environment, icebreakers were used, such as playing each presenter’s favorite motivational-themed song prior to presenting and dressing up occasionally for themed days such as Rodeo Day.
“This team was just so great at lifting each other up,” Carroll said.
Personality tests, or what is called the CliftonStrengths Assessment,2 were also part of the planning process so people understood how each other communicated and whether they were high-energy, for example, or more analytical.
At times, more than 50 people were on Zoom calls in the “Virtual Big Room.” About 75 Page employees contributed throughout the duration of the project. COVID-19 resulted in more team members observing meetings where, prior to COVID-19, they would hear secondhand from project managers. A Playbook outlining the team and logistics was developed to ensure new team members felt comfortable.
“Being able to hear firsthand allowed them to work immediately on revisions and understand the context for the design revisions,” Carroll said.
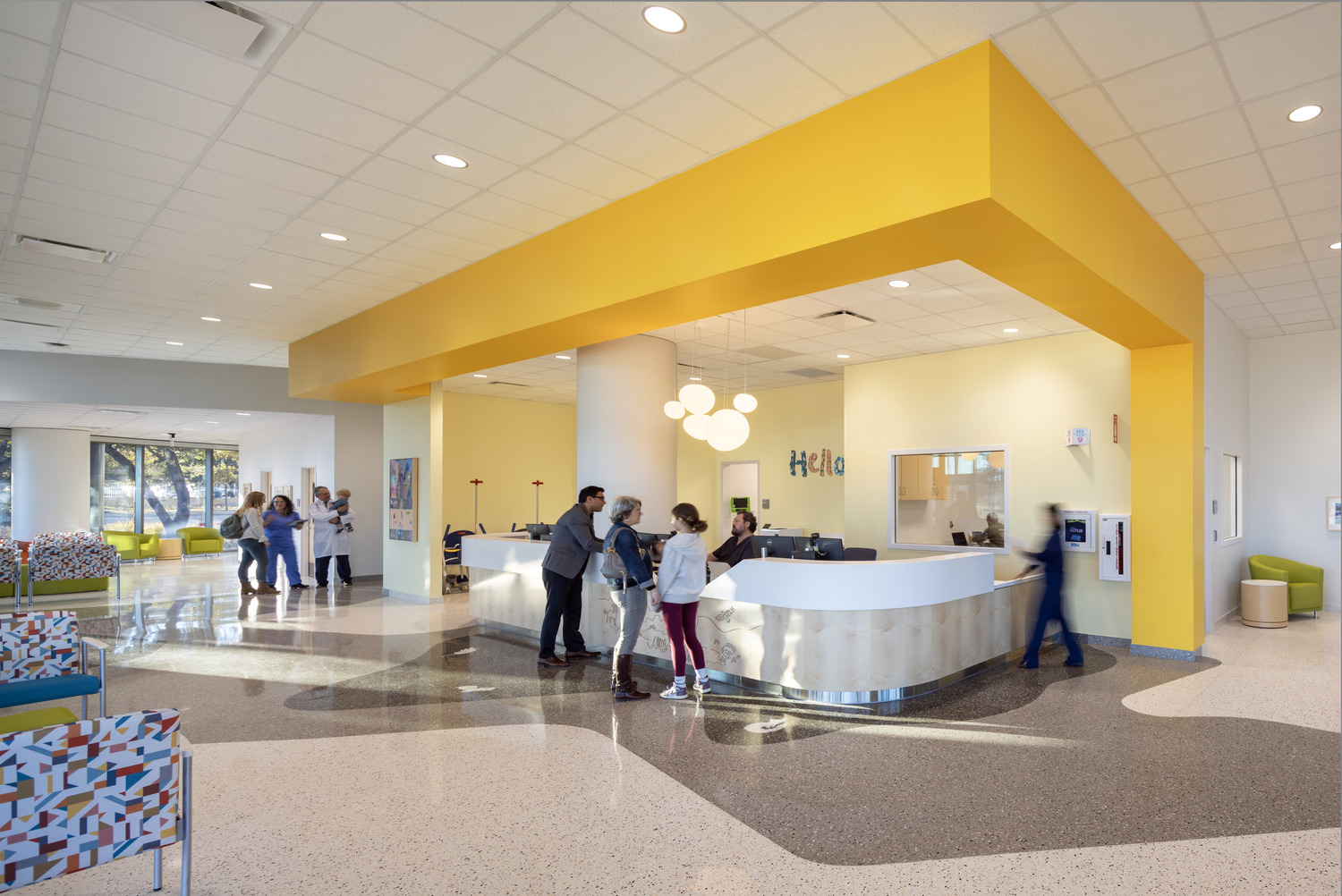
Innovative design solutions driven by collaboration
Using various techniques, the team was able to monitor tasks weekly, cross out what was being completed, and monitor budget and construction costs.
“Lean becomes embedded in how you work day-to-day, as well as how you communicate with people both verbally and visually,” Carroll explained. Page also invoked the Ripple Intent communication tool, which focused on respecting the strengths and differences of individuals and was a complement to Lean.3
Collaboration tools used during COVID-19 resulted in positive design performance results, with an eye on flexibility for future spaces. Some of those key design innovations included:
- Isolation units on the inpatient floors with expanded ability during a pandemic.
- Drive-up testing locations adjacent to the primary care clinic.
- Improved access to the lab and retail pharmacy near the main entrance for quick in and out service.
- Personal Protective Equipment (PPE) areas for suit-up before entering exam or patient rooms.
- Entry vestibules designed for ‘pop-up’ screen detection for body temperature scanning.
- Expanded patient rooms for families, family lounges, and kitchenette areas.
- Enhanced technology and monitors in rooms to communicate with family members who may be unable to visit.
- Outdoor therapy respite space.
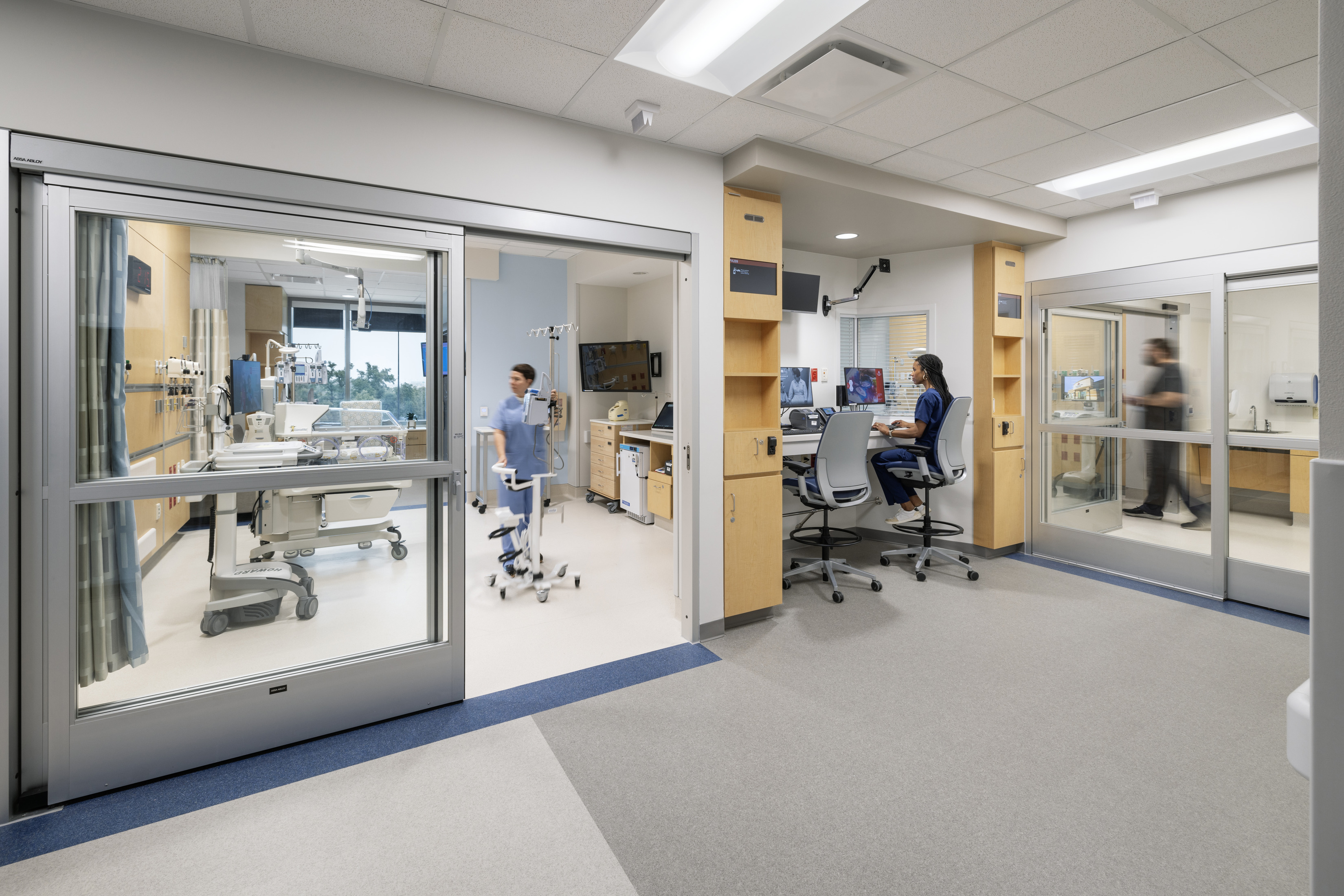
Sustainability at the forefront
Despite the pandemic-related challenges, the team remained committed to sustainability. Their innovative efforts during the pandemic resulted in various awards, including Texas Children’s Hospital North Austin Campus receiving the 2024 National Design Award from the Lean Construction Institute for the quality of work performed on time and under budget despite the pandemic, supply chain interruption, and high inflation.4 Making decisions early, such as pre-buying materials before supply chain issues, led to those results.
Energy savings, which resulted in the hospital campus receiving a 3-star rating with Austin Energy Green Building,5,6 included:
- An annual energy savings of 24%.
- A 23% reduction in annual indoor water usage.
- Over 35% of the materials, by cost, were sourced from recycled content and/or Texas suppliers.
- Over 75% of construction waste was diverted from landfills.
- 100% LED interior and exterior lighting.
- Instituted a robust recycling program that included electric vehicle charging stations for staff and visitors.
- Locally sourced produce and composting in commercial kitchen and dining areas.
- Protected existing trees; planted over 150 new trees and placed them strategically for shading.
- Reconstructed wetlands to manage and treat at least 50% of stormwater onsite.
“Being mindful of where the building was positioned and how we were going to expand the building in relationship to the site was a priority,” Carroll shared. “Coming onto the site, some of the first things you see are trees and the water.”
The campus design uses locally sourced limestone to reflect the Central Texas landscape, like the building’s exterior.7,8 Austin's unique culture and geography are also featured inside, with artwork of caverns, aquifers, and wildlife, allowing for interactive play for children and an uplifting feel for healing and recovery.
A blueprint for the future
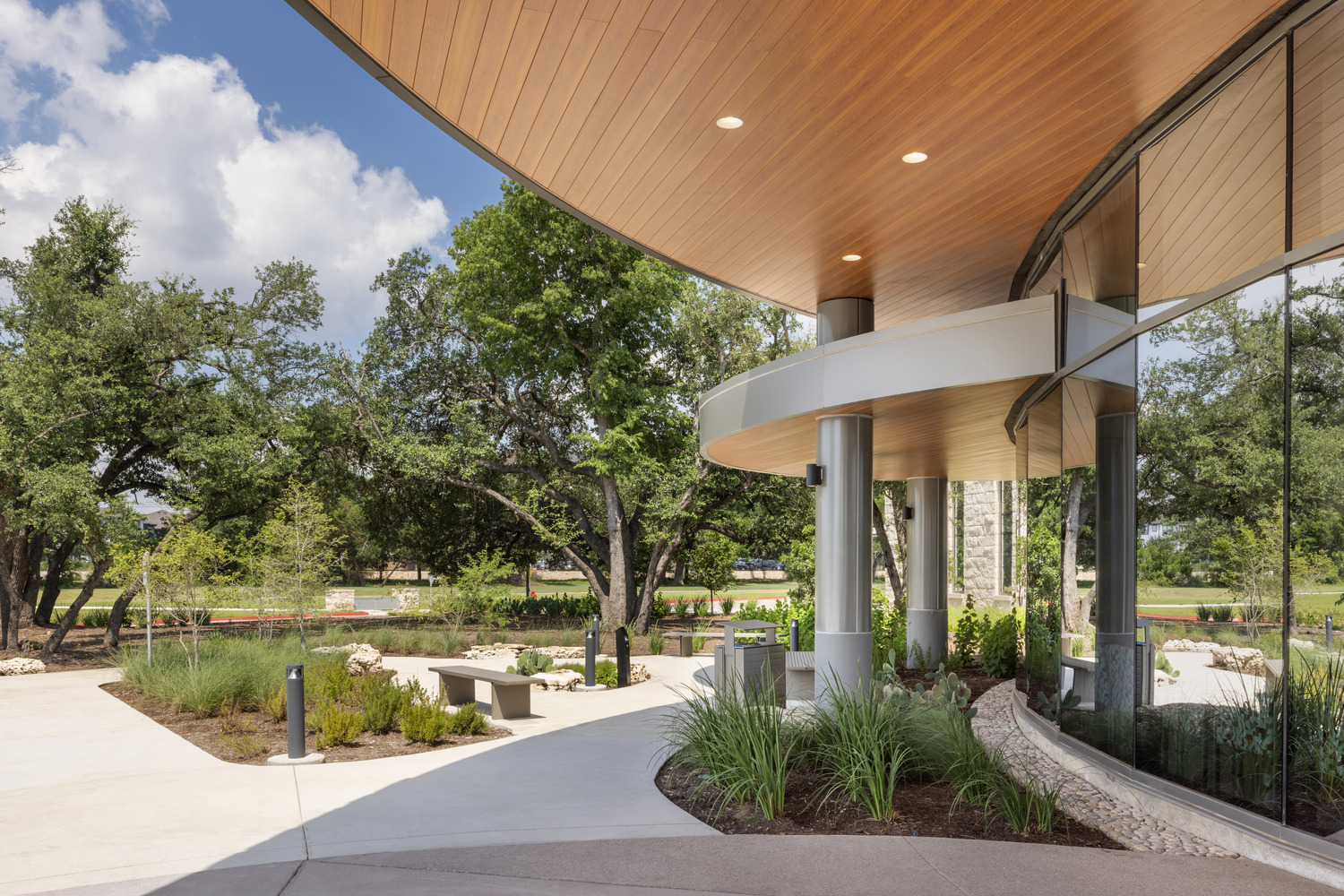
The Texas Children’s Hospital North Austin Campus exemplifies how resilience, innovation, and Lean methodologies can drive project success, even in times of crisis. The pandemic accelerated a shift in how teams collaborate, problem-solve, and leverage technology, insights that now shape the future of healthcare design. As the industry moves forward, the true measure of leadership lies in the ability to adapt, embrace change, and turn challenges into opportunities for smarter, more efficient, and human-centered solutions.
Looking ahead, Page continues to incorporate lessons learned from COVID-19 into future projects, including ongoing work at the children’s hospital.
The importance of resiliency is one of the biggest takeaways for future projects.
“I think the positive change we have to remind ourselves as we get back to pre-COVID [lifestyle] is connecting on a human level,” Carroll said. “Just keeping that culture as we move to other projects. After COVID-19 [faded], everything tried to go at lightning speed to catch up. But I think COVID-19 forced us to slow down a little bit to get to know each other and work towards shared goals. Slowing down and getting to know each other created comradery and efficiency in meeting and exceeding the project goals.”
Deborah Circelli is a freelance writer with marketing experience in the healthcare, space and higher education fields. She previously wrote for newspapers throughout Florida.
References:
- Toyota Production System. Available at: https://www.lean.org/lexicon-terms/toyota-production-system/
- CliftonStrengths Assessment. Available at: https://www.gallup.com/cliftonstrengths/en/252137/home.aspx
- Ripple Intent. Available at: https://rippleintent.org/about-us/
- Announcing the 2024 LCI Design Award Winner. (2024.) Lean Construction Institute. Available at: https://leanconstruction.org/blog/announcing-the-2024-lci-design-award-winner/
- Building a Sustainable Future at Texas Children's Hospital. I+S Design. (May 1, 2024.) Available at: https://www.iands.design/videos/video/55036325/building-a-sustainable-future-at-texas-childrens-hospital
- Austin Green Energy Building. Available at: https://austinenergy.com/energy-efficiency/green-building
- How the Texas Children’s Facilities Planning and Development Team Designs Patient-Centered Spaces. Texas Children’s Hospital. (Oct. 23, 2024.) Available at: https://www.texaschildrenspeople.org/facilities-designed-for-healing/
- Texas Children’s Hospital Reaches Major Milestone in Expanding Service within the Central Texas Market. Texas Children’s Hospital. (May 16, 2022.) Available at: https://www.texaschildrens.org/content/news/texas-childrens-hospital-reaches-major-milestone-expanding-service-within-central